In 2016, I built my first 3d printer, the Tripledoomtopus, a custom Delta-style machine made of MDF and aluminum. The original idea was to minimize printed parts and create a printer that could self-upgrade later without this limitation. This post is about the second iteration and how I addressed its growing list of problems.
Problems to Fix
Over the years, I identified several issues that needed attention:
- Stepper motor mounts: PLA parts were breaking under strain.
- Extruder design: Lacked torque and struggled with some filaments.
- Arm bearings: Ball bearings were off-center with the carbon tubing.
- Maintenance: The risk of "explosive disassembly" made working around the hotend nerve-wracking.
- Electronics: My DIY Smoothieboard worked, but it required too much wiring, and the firmware was no longer being supported.

Goals and Features
Here's what I set out to achieve in this second iteration:
- Add a modular head for tool swaps.
- Upgrade to dual nozzles.
- Use a geared extruder for better torque.
- Replace the old Xbox 360 power brick with a proper PSU.
- Use stronger PETG parts for critical components.
- And, of course… LASERS.
Explosive Dissassembly
Yes, it's as dramatic as it sounds. The spring-loaded arms were rock solid... until the hotend hit something. One time, I left the printer door open, and an arm flew three meters away during a print.
To mitigate the damage, I added a "safety clip" between the head and one arm. If the clip detaches, the printer pauses and shuts off all heaters. This at least saves filament and prevents further destruction.
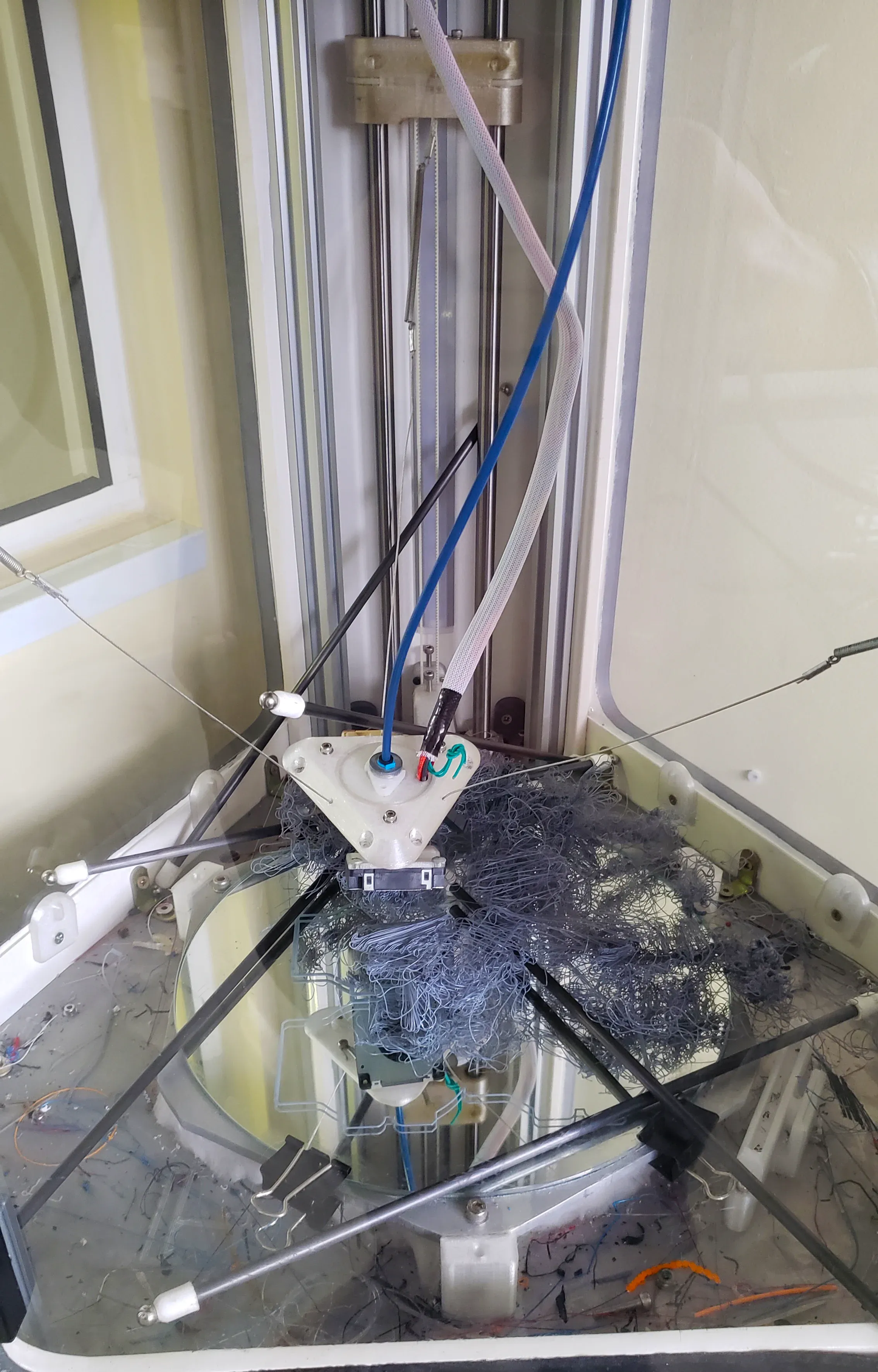
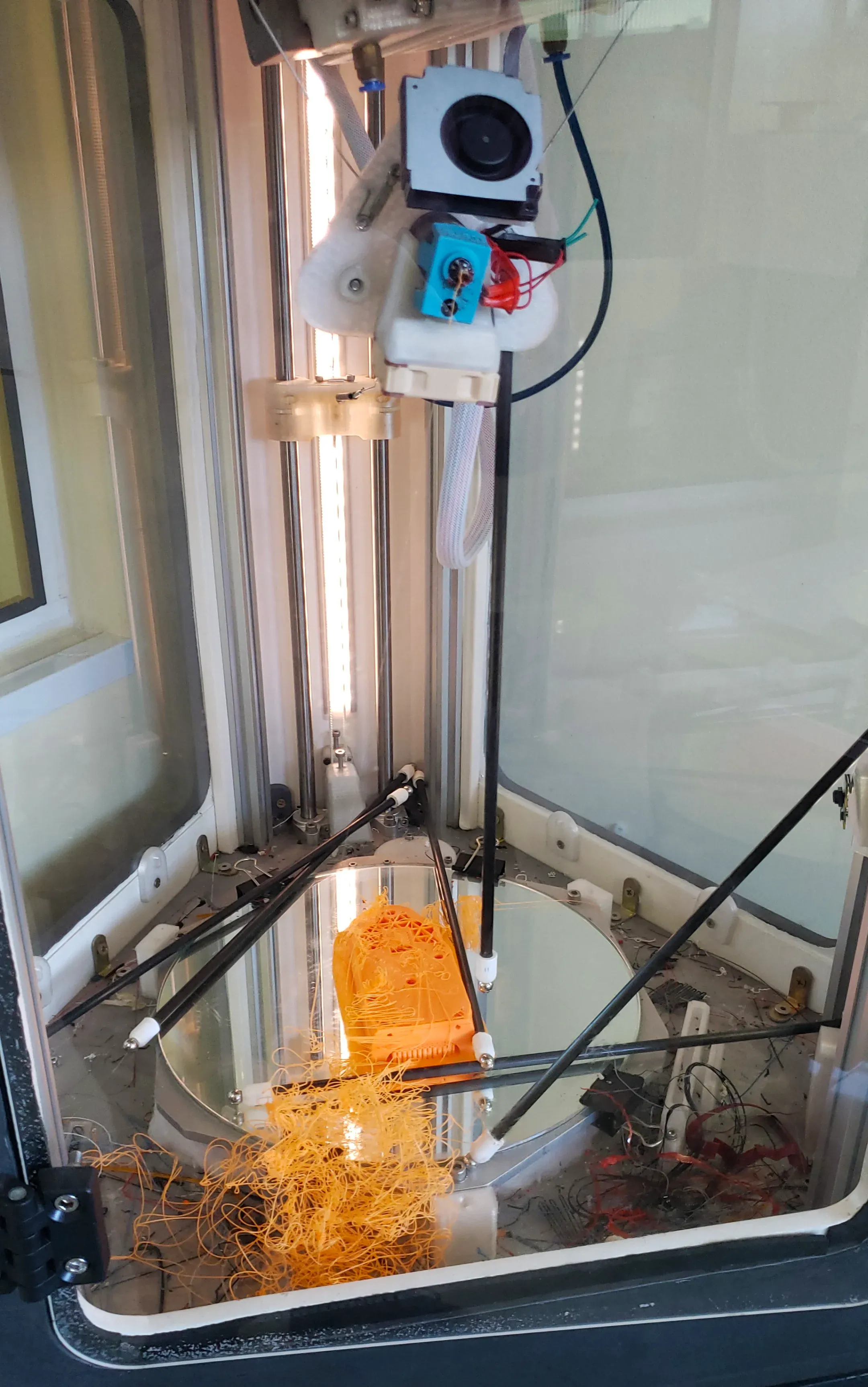
Modular Toolhead
I implemented a detachable umbilical cord with a custom connector. Swapping toolheads was simple, just unscrew three M3 screws and detach the tool. Over its lifetime, I made three toolheads:
- Printing head: E3D V6 Hotend with a blower fan for part cooling and a 40mm fan for the hotend heatsink.
- Z-Probe: A hall sensor for bed leveling. Due to the printer's sturdiness, I only needed it 2~3 times.
- Laser engraving head: A 405nm 500mW laser diode for engraving experiments.
One toolhead that nearly happened was a drilling head with a small DC motor for PCB drilling after etching. However, I avoided milling because of the high risk of unplanned disassembly.
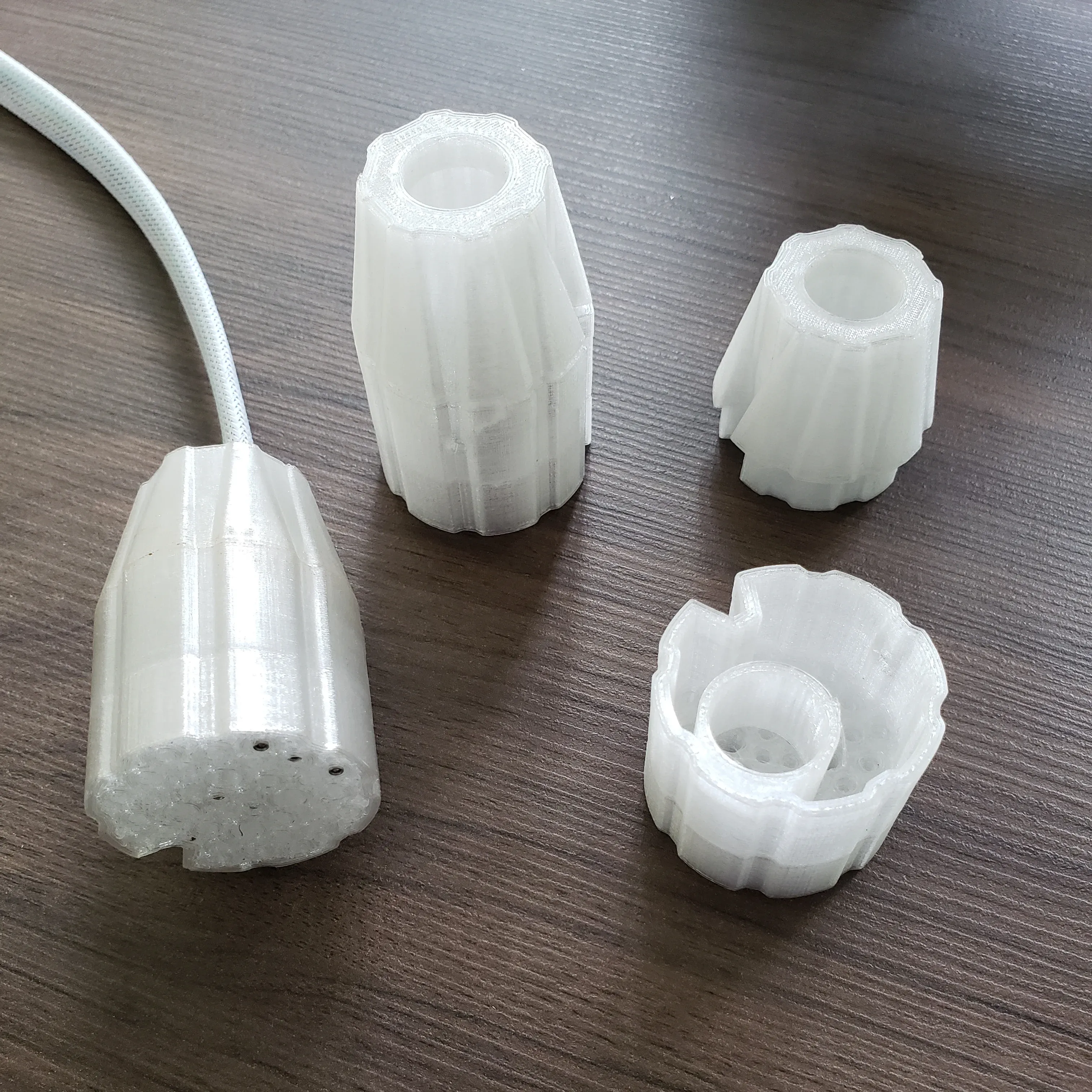
Internal ring holds the braided cable in place.
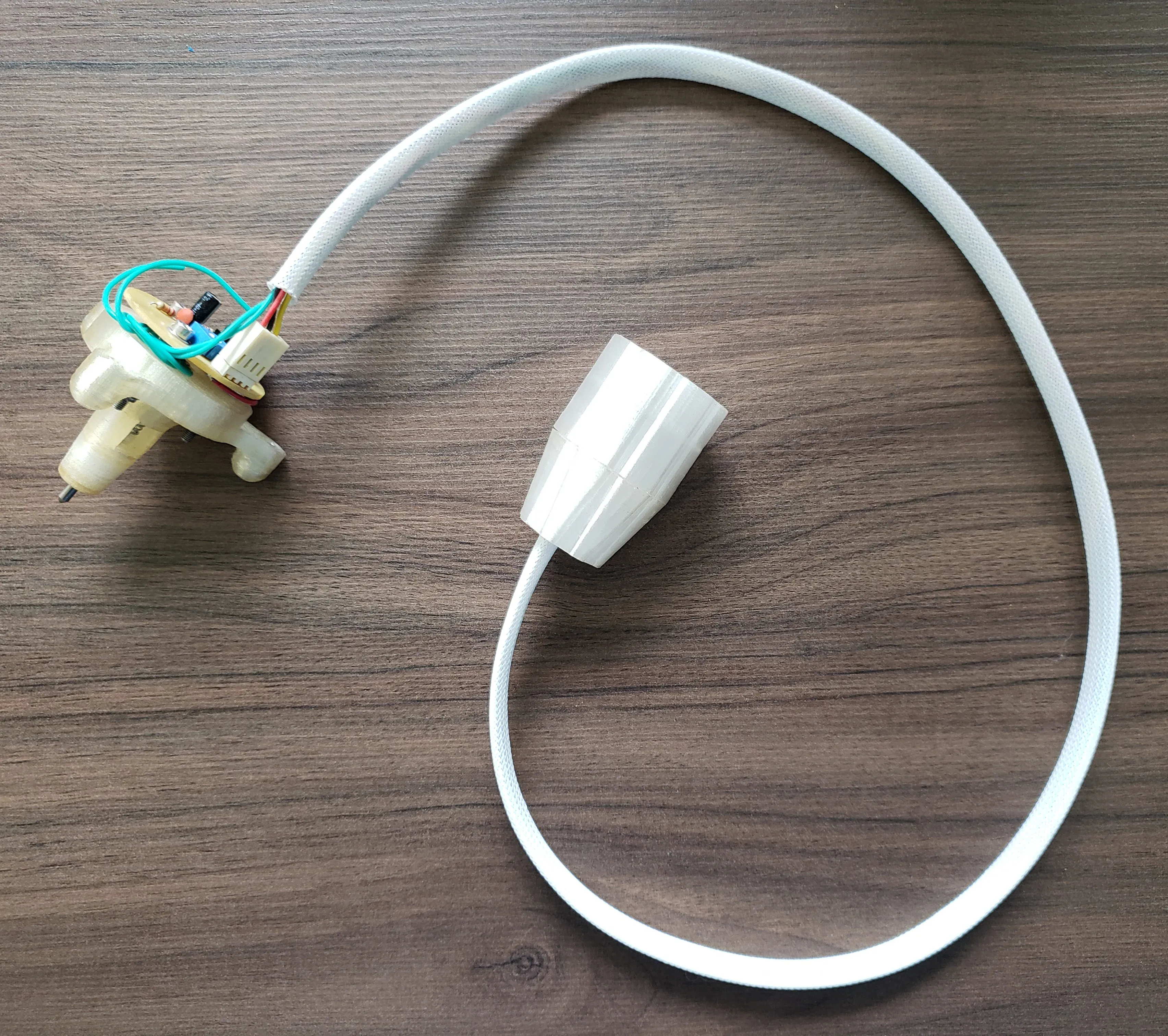
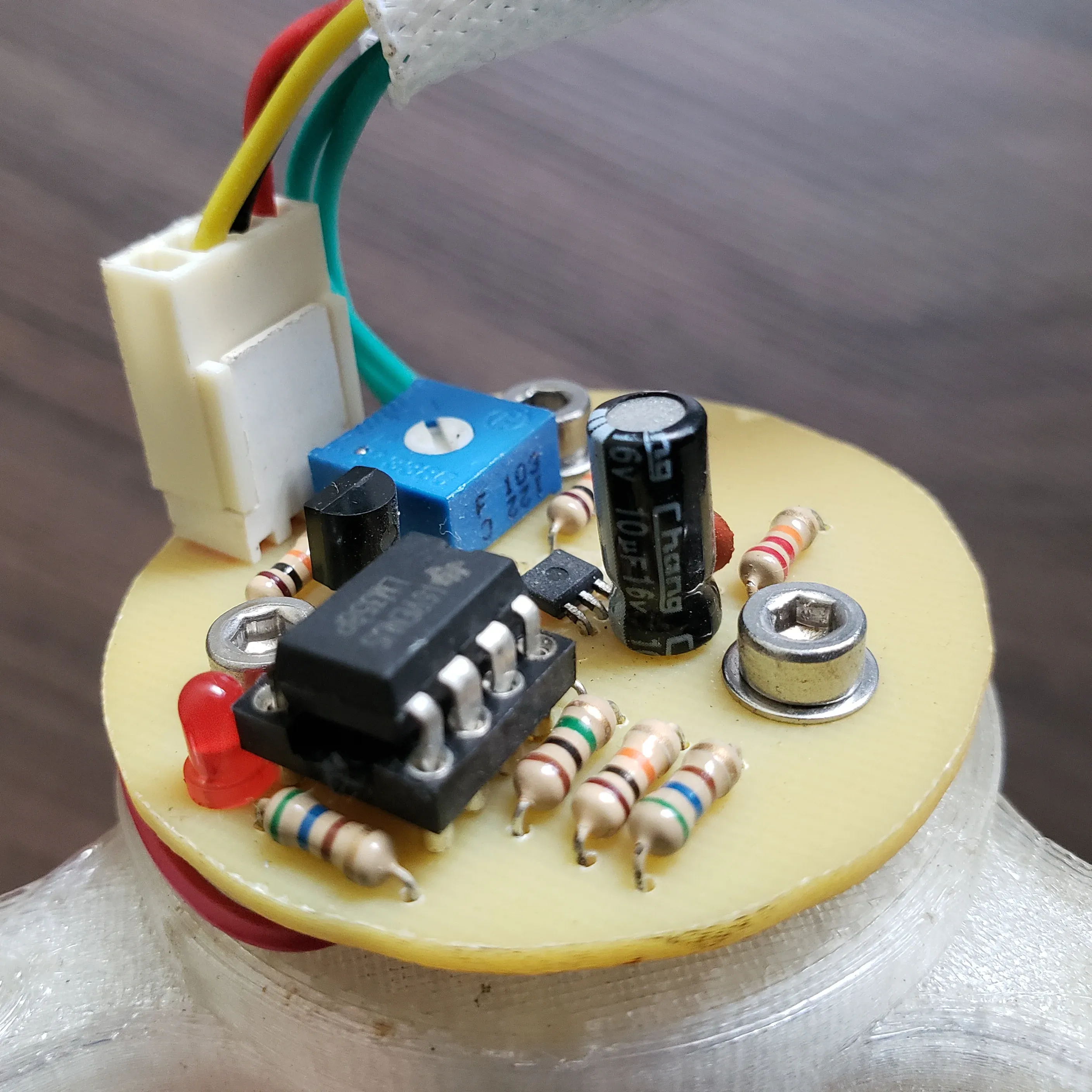
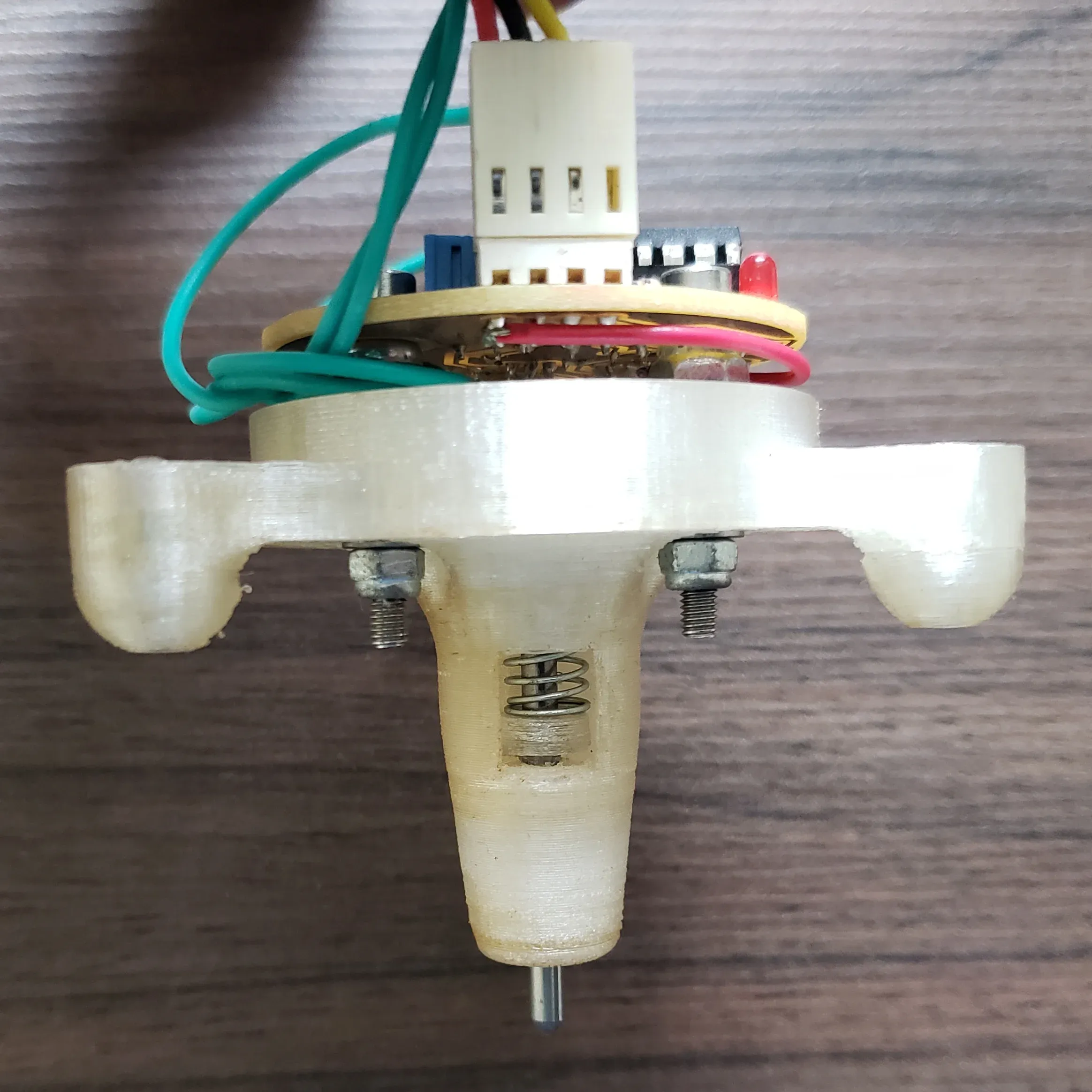
Electronics
The Smoothieware project was becoming inactive, so I swapped my DIY Smoothieboard for a Duet 2. This change significantly cleaned up the electronics bay by reducing wiring.
I upgraded the power system to 24V with a Meanwell PSU, adding:
- A step-down converter for 12V components.
- A secondary 5V Meanwell PSU for the Raspberry Pi with Octoprint and the WRGB led strips.
- A master relay to shut down the 24V PSU.
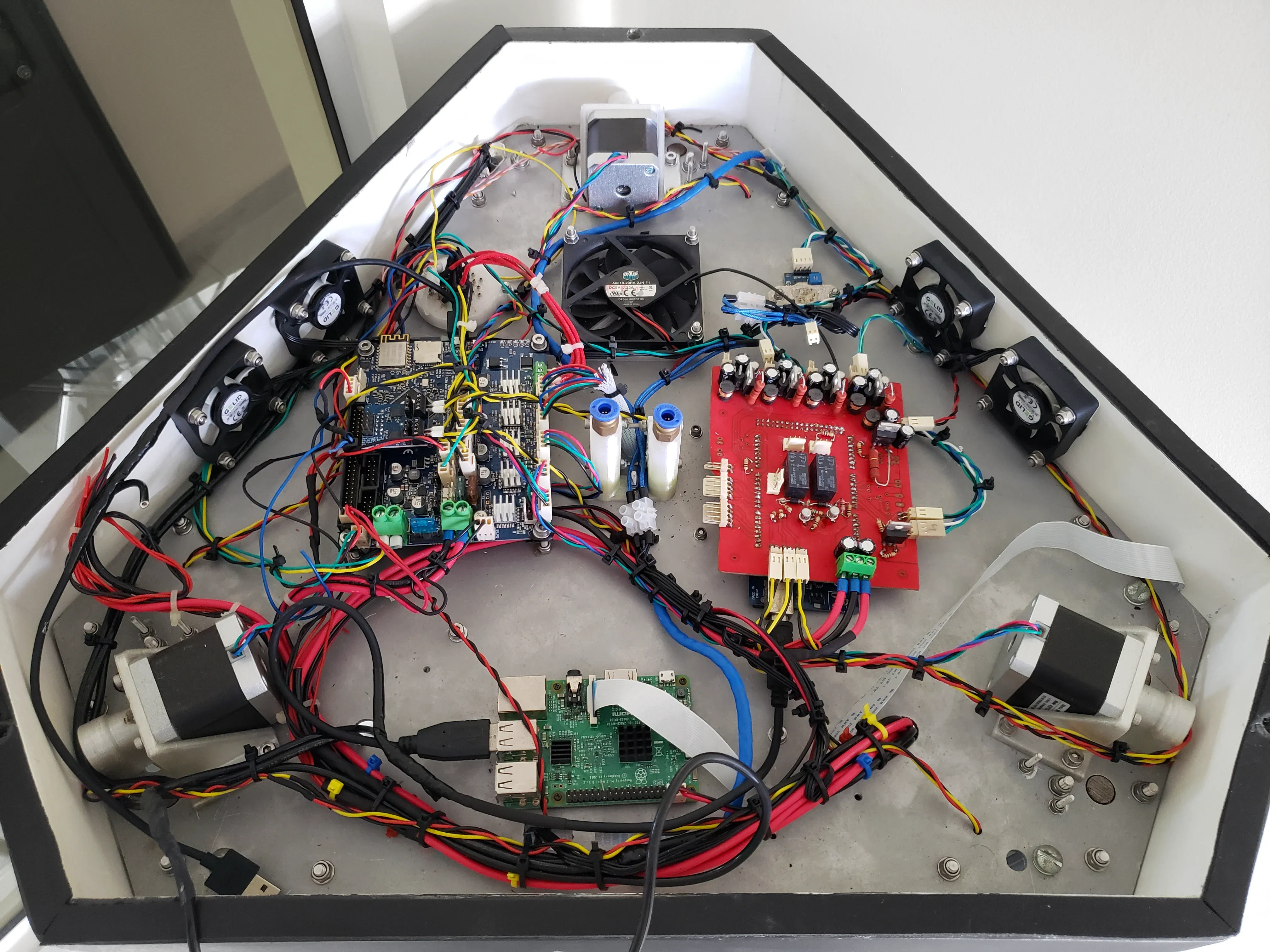
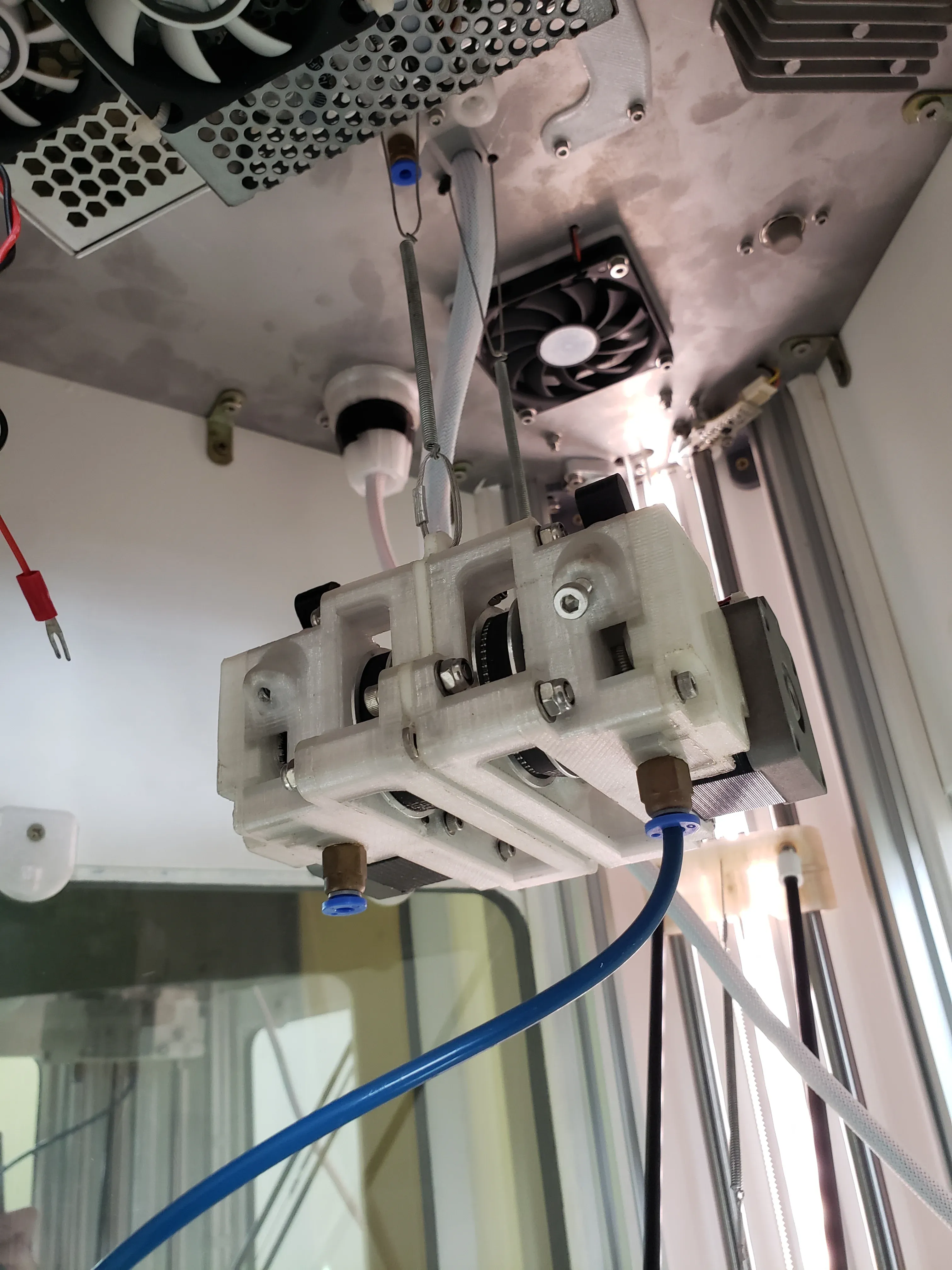
Hanging Dual Extruder
Although I didn't add a second hotend, I had a spare stepper motor and expected to eventually do something using both. The idea to go with a hanging extruder had two purposes, to reduce the bowden tube length, and to make maintenance easier by allowing me to move the extruder freely. I ended up going with a mirrored design and using a belt drive to achieve a 4:1 gear reduction. There's also a small brush to the other side of the drive gear to remove any leftover plastic bits that might get grinded away during extrusion.
Laser Engraving
With the modular toolhead system, I experimented with laser engraving using a 405nm 500mW laser diode.
For safety, I used proper laser glasses and replaced the aluminum surface with a wasteboard cut by a friend. While I didn't explore this much, it was a fun and useful experiment.
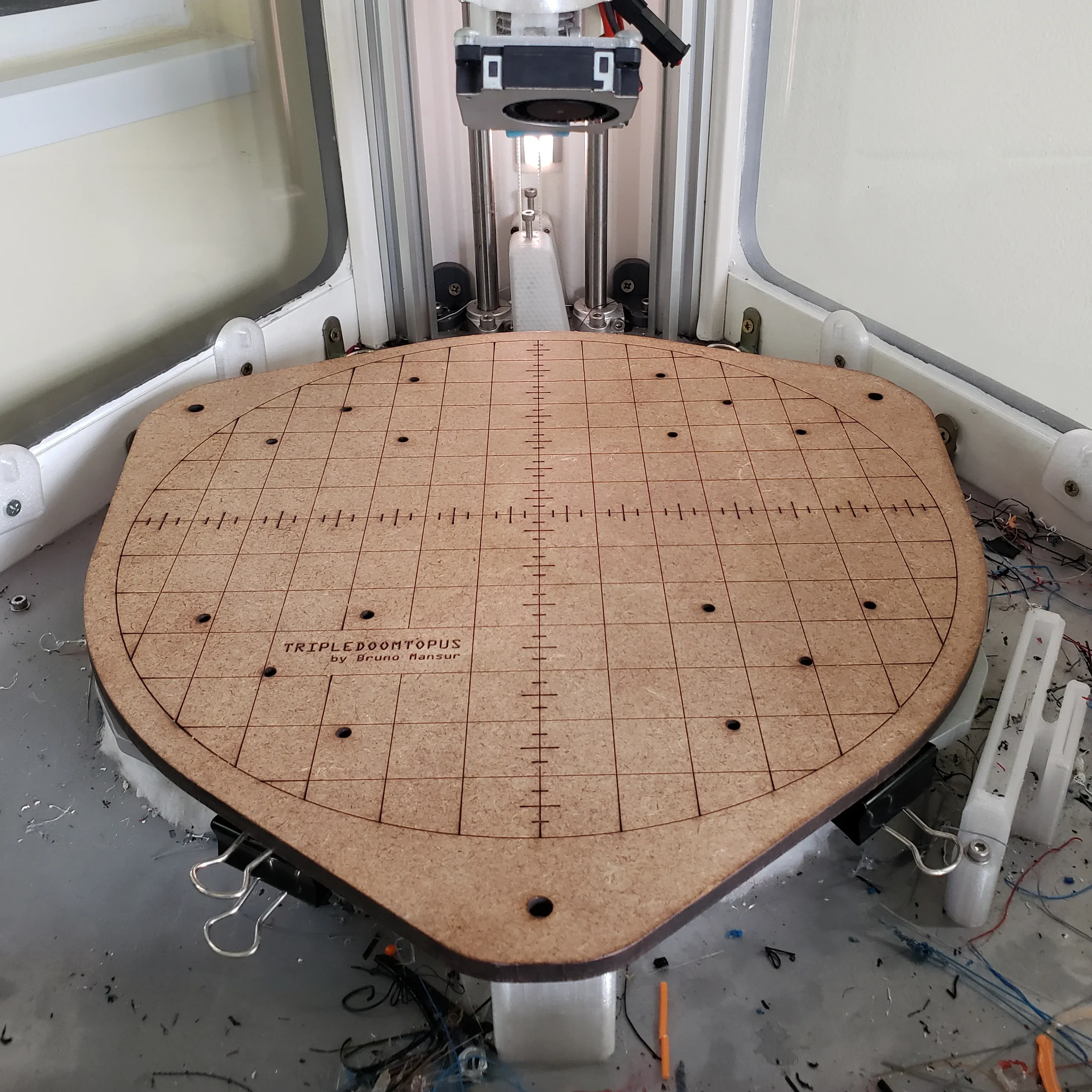
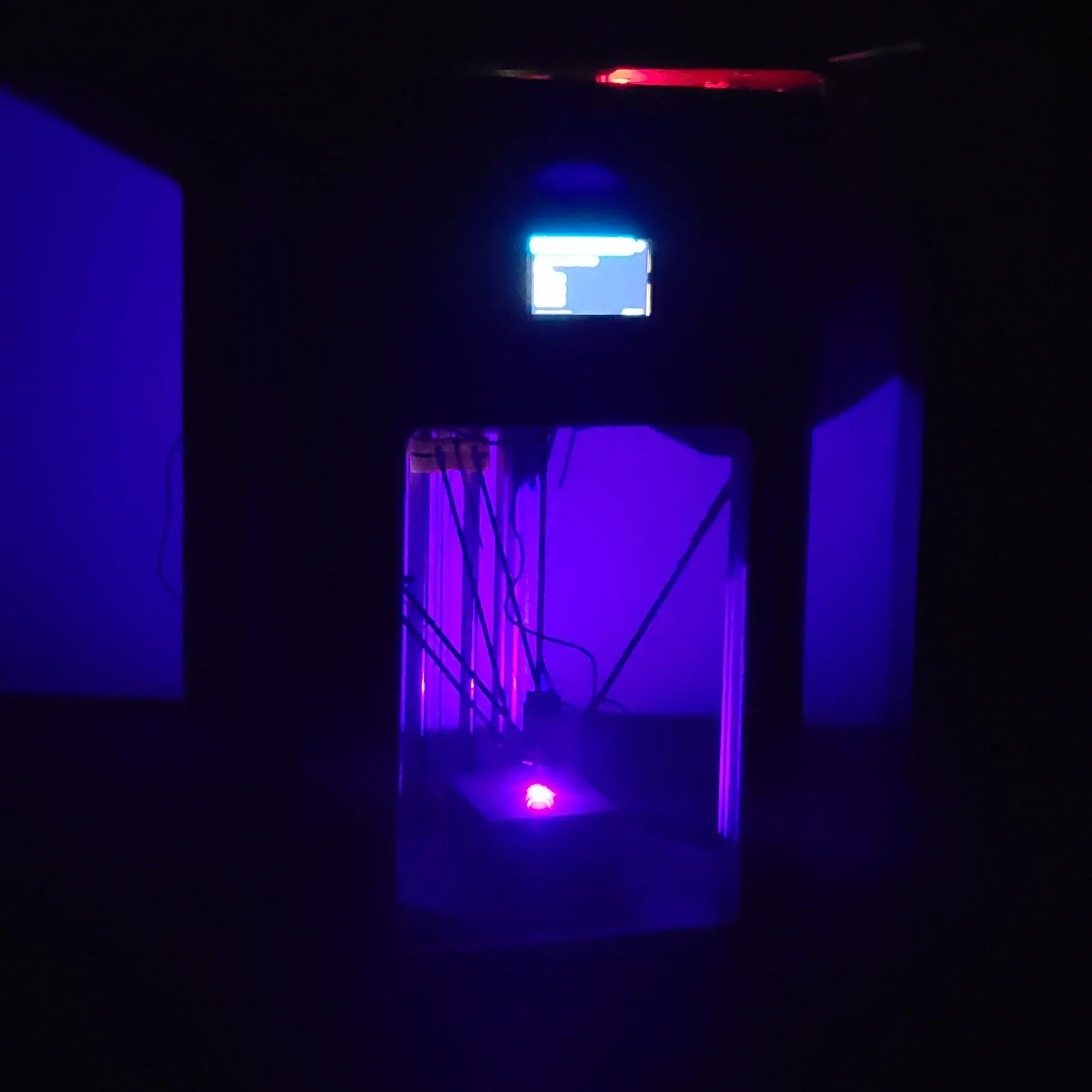

Wrapping Up
This second version of the Tripledoomtopus served me well and taught me a lot about 3D printing. However, the design wasn't without flaws... The spring-tensioned arm design combining steel wire, springs, and screw eyes made it creak like it was about to break. The empty internal space of the Delta printer also acted as an echo chamber, amplifying the noise.

By late 2021, I decommissioned it completely when I moved abroad. It was so heavy I could barely move it. Ironically, despite its quirks, I never had to recalibrate it, not even after bumpy car rides.
I'll miss it.